@Frostnipped Todger
Ive been forging for years for sale.
I have a coal forge(for damascus) and gas forge(for everything else).
I have a 60kg anvil with a 30kg sand basin stand block that i paid and was asshurt about the price afterwards until i used it.
For starters il lay some things out.
Anvil:
You dont "need" a face hardened professional anvil, but it makes a big, BIG difference.
You can work with a cheap 30kg chinesium anvil but you need to round all the edges.
Railroad track works great for knifes, because its face hardened. The issue with using railroad track is that an anvil sized piece doesnt weigh enough so it gives you "bounce back" on the workpiece, buuut you can help with that by having a heavy base block and you HAVE TO secure the track piece to the block really tightly.
Hammer:
Just get a 4 or 5 pound hammer. BUT you need to round the edges on most hammers to forge. Why? Because if your strike face isnt perfect youl hit with the edge and leave a sharp "dent" into the material instead of shaping it.
Blade material:
I personally use 80crv2 for everything and 15n20 when i make damascus.
I started with car leaf springs, its pretty good for making knives out of.
If youre gonna make a knife by "barstock removal" you first need to forge the spring straight, then back into the forge for few minutes untill its "quench hot" and then let it aircool to normalize it.
Otherwise youre just working with a hard material, and since that spring has been working for years in a car there is internal stress in the piece, so if you dont normalize the piece, it will warp when you quench it.
Most "blade steel" sold like 1095, 80crv2 etc etc in some point in its lifespan has been rolled into a steel roll for transportation, then before its cut into smaller pieces its often "cold rolled" to be straight again. Itl come out all warped as fuck sometimes when you quench it, so you should normalize that steel too before quench.
Old metal files are great, theyre usually in the upper end in carbon content so they will harden really well but theyre also more brittle.
And DO NOT FUCKING LEAVE THE FILE TEETH IN THE KNIFE! Youre just creating hundreds of sharp stresspoints where the blade will snap way, way easier than a straight surface.
What you need to do before forging is to normalize the file, then grind away the teeth, THEN forge, you cant really forge the teeth away.
You probably shouldnt use modern files because theyre often very high alloyed metals and that comes with, more extensive heat treatment.(soak times, you need to be really accurate with temperatures, and you need to cycle the tempering.
Well you can do it like "normal" but you wont get the properties of that mixture, and your piece might be left brittle.
One downside of using files is getting a file that someone had thrown once, so when you go to quench it you see a large but very thin crack somewhere in the blade.
As a material id recommend basic bitch 1085.
Why?
Because its really forgiving with quench temperature + its cheaper than other knife steels.
And since youre always using the same steel, you always get predictable results.
Once youre confident in your heat treatment process, id start using 80crv2.
Its almost double the cost however.
Its a low alloy steel but that alloying makes the stuff really, really tough while still being hard.
If youre shopping for the "high end super steels" as a starter, dont.
Stuff like Elmax or Apex Ultra gives you really, really hard blades that dont lose sharpness easily, but theyre brittle as shit so if you intend to "baton" something like a log with your knife, NOPE its just gonna shatter.
Just one look at the high end metals datasheet for heat treatment process shows you how accurate you need to be with thermal cycles, soak times, tempering and temper quenches.
Same goes for most stainless steels, the quench temperature is often like +/- 10 celcius, if you go above that, too brittle, below, too soft.
They arent forgiving.
Forge:
Gas, yeah get a gas forge...
Any person seething about "BUT YOU GONNA BURN THE CARBON OFF!" is a retard who has been using a shitty gas forge thats over aired and doesnt have air flow adjustment.
Youre less likely to overheat your steel with a gas forge.
A coal forge when using coke will very easily melt your steel by accident.
Oh and, always round your sharp corners, if you dont the blade will snap easily.
This is something i read some time ago about stress points.
Ive been making knives for years, only recently ive moved to high end pieces.
Usually making the blade is the least time consuming part for me, if a blade takes me few hours to forge, heat treat, grind and polish, the handle and sheathe take me 20-30 hours.
for refrence:
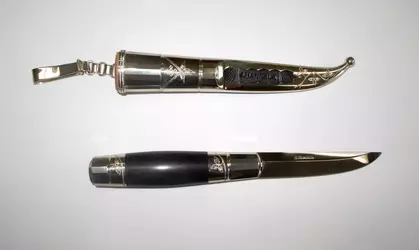
Not mine, but my last piece was one like this.(mine is stamped with my initials, aint gonna selfdox).
TL;DR gas forge, 4 pound hammer, railroad track or chinesium anvil, gas forge, 1085 or car leafsprings/metal files.
The easiest way to learn is to learn from someone, atleast where i live forging classes are held all over the place, usually 20-30 hours total for a whopping 75 bucks.(theres usually 5-10 people at once)