- Joined
- Dec 12, 2022
Part 1: The Beginning
It seems like quite a few of you from a Q&A I did were interested in welding, so here we go. This shall be split into parts, as there's a lot of shit to go thru.
So what is welding? Where did it come from? Why are we here? I can't answer that last one but I can the first two. Welding in its simplest form, is the fusion of metal. There are many different forms, and many auxiliaries that go into the process, but just for welding at its most basic, we have MIG, Stick, TIG, and Flux-Core, along with Oxy Acetylene cutting and plasma cutting as a nessicary part of the process.
Now where did we start? Late 1800's with the invention of the oxy acetylene torch and the harnessing of electricity. And soon came Carbon Arc welding, later turning into carbon arc cutting.
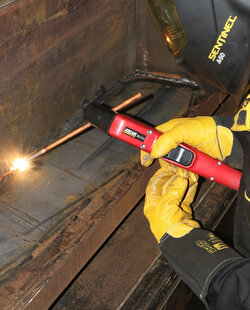
Originally it was used for welding but... it was shit. Dumped way too much carbon into the steel. Later it was adapted into a cutting tool with the addition of compressed air, able to remove welds. Also used in giant street lamps for a time.
Next came Stick, basically a rod coated with a Flux coating meant to keep airborne contaminates out. Now this worked, and is still used to this day, and first major application was WW1.
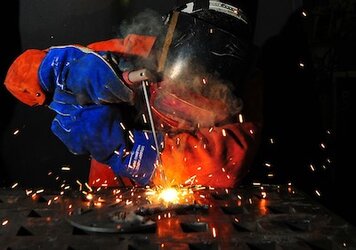
But stick is dirty, hard to use, and slow. It can work in all positions, but a evolution was needed. Meet MIG. The wire gun you're probably somewhat acquainted with. Much less of a skill ceiling and greater speed, uses gas to keep out contaminates, it's basically a glue gun, but at the cost of deposition rate and some strength compared to stick.Nevertheless, WW2 put it to use, most notably on the Sherman tank. This is also when rivets started dying.
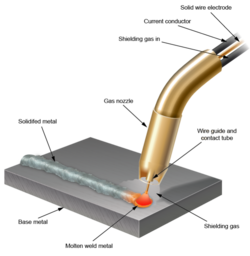
Next is TIG which came around about at the same time. Uses a tungsten electrode to focus electricity onto a small point and is notably used on Aluminum, Stainless Steel, even things like Titanium. It is the Mac to the PC in the welding world. Strong as stick, can weld pipe, but requires high skill.
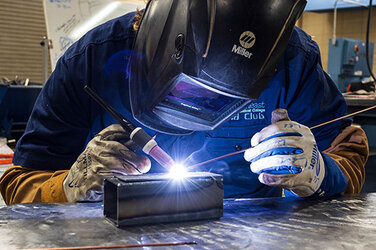
Finally for the main welding processes on this timeline, we have Flux-Core. Combine the wire feed system with the deep penetration and deposition rate of stick, along with the unique option to use gas, and you get Flux-Core, the newest kid on the block. It has slag like Stick, but it's much easier to pound off. It's gearing up to replace stick in the next few decades.

So this is the bare basics on where welding came from and the processes. I'll be posting updates as we go along, but feel free to post your welds, takes, questions, whatever. Until then thanks for reading!
It seems like quite a few of you from a Q&A I did were interested in welding, so here we go. This shall be split into parts, as there's a lot of shit to go thru.
So what is welding? Where did it come from? Why are we here? I can't answer that last one but I can the first two. Welding in its simplest form, is the fusion of metal. There are many different forms, and many auxiliaries that go into the process, but just for welding at its most basic, we have MIG, Stick, TIG, and Flux-Core, along with Oxy Acetylene cutting and plasma cutting as a nessicary part of the process.
Now where did we start? Late 1800's with the invention of the oxy acetylene torch and the harnessing of electricity. And soon came Carbon Arc welding, later turning into carbon arc cutting.
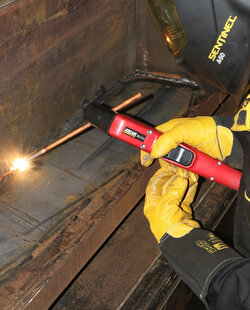
Originally it was used for welding but... it was shit. Dumped way too much carbon into the steel. Later it was adapted into a cutting tool with the addition of compressed air, able to remove welds. Also used in giant street lamps for a time.
Next came Stick, basically a rod coated with a Flux coating meant to keep airborne contaminates out. Now this worked, and is still used to this day, and first major application was WW1.
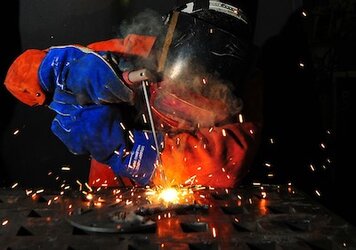
But stick is dirty, hard to use, and slow. It can work in all positions, but a evolution was needed. Meet MIG. The wire gun you're probably somewhat acquainted with. Much less of a skill ceiling and greater speed, uses gas to keep out contaminates, it's basically a glue gun, but at the cost of deposition rate and some strength compared to stick.Nevertheless, WW2 put it to use, most notably on the Sherman tank. This is also when rivets started dying.
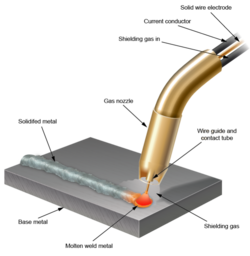
Next is TIG which came around about at the same time. Uses a tungsten electrode to focus electricity onto a small point and is notably used on Aluminum, Stainless Steel, even things like Titanium. It is the Mac to the PC in the welding world. Strong as stick, can weld pipe, but requires high skill.
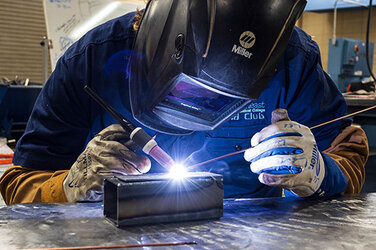
Finally for the main welding processes on this timeline, we have Flux-Core. Combine the wire feed system with the deep penetration and deposition rate of stick, along with the unique option to use gas, and you get Flux-Core, the newest kid on the block. It has slag like Stick, but it's much easier to pound off. It's gearing up to replace stick in the next few decades.

So this is the bare basics on where welding came from and the processes. I'll be posting updates as we go along, but feel free to post your welds, takes, questions, whatever. Until then thanks for reading!
Attachments
Last edited: